Wrong Tool, Right Tool
- John Gardner
- Feb 20, 2022
- 3 min read
If you are a landowner, a utility manager, or someone who wants aerial survey of your assets; it is vital to choose the right tool for the job. And before you can do that, you’ve got to ask yourself some questions:
What information do I need?
Where is the location?
What is the size and scope of the project?
How quickly do you need the information?
What is the budget?
Here are three scenarios that show how different tools can be deployed for different jobs, and what customers should consider when thinking through the tasks at hand.
Scenario A:
A farmer named Bill has contacted us about mapping damaged crops due high winds and storms. His insurance company needs accurate information measuring the area of crop damage. The location is Northeast Arkansas, flat terrain and rural. He needs this information as soon as possible, a week at the latest. And he doesn’t have a lot of money to spend.
This sounds like a perfect job for a smaller drone to do some photogrammetry work. This is relatively inexpensive compared to other methods. The drone can quickly scan the crops, identify the damaged areas, then create a 3D map. After processing, he could have everything he needs the next day. This job will probably end up costing about $2000.
What if he picked a helicopter company to come out and do lidar? These kinds of jobs are incredibly expensive and the turnaround time for lidar takes months. Depending on the helicopter, this job could cost him $20,000 - $100,000.
Scenario B:
A natural gas pipeline Manager named Vicky wants to start patrolling a pipeline once a month. The purpose of this patrol is to gather any information about the conditions of the ROW. This line is 300 miles long and crosses through some rough and diverse terrain. Access can be very difficult. This report must be submitted as soon as the patrol has been completed.
Would this be a good job for a drone? Probably not, considering the turnaround time. Yes, the drone can gather all the information they need, but the length of the pipeline and the terrain would make this job painstakingly slow, and the cost would be very high.
An airplane would be a good choice for this job. An airplane could finish this patrol in a few hours and gather all the required information. The cost of this could be around $1500 per patrol.
A better choice would be a helicopter, because the helicopter inspects the line lower and slower than the airplane, adding to the quality of the inspection. Also, if a property owner were digging an irrigation line towards the pipeline, the helicopter could land and stop the landowner before they cause damage to the line and themselves. The cost for this will be around $3500 per patrol.
Scenario C:
Steve with Powerline Company of the World, Inc. requested that we perform a detailed inspection of a section of his powerline. That line section is 70 miles long and located in the mountains. There are nearly 300 steel towers to inspect. He isn’t too concerned about getting this information right away. Steve has always performed this job with a helicopter but wants an estimate with a drone.
So due to all the information Steve provided us, a helicopter is absolutely the right tool for the job. A good helicopter crew can inspect an entire structure in about 4 minutes. Therefore, the helicopter is going to cost about $16,000 to do this job.
Steve also said he wanted this priced out for a drone. There will be a 2-man crew - pilot and VO. They’ll need a 4x4 truck, UTV and trailer to get access to VLOS (visual line-of-sight) areas. An unmanned system will need to hover at each structure for extended periods of time to capture the data needed. So, I would say a drone crew might be able to get 2 structures done in an 8-hour day. You are looking at about 1,128 crew hours to get all the photos and videos done. If you were to pay each of those guys $20 per hour, that’s $45,120 for that inspection. All things considered; I estimate about $200,000. That should cover all insurance, equipment, post processing, data management, travel and per diem. And if only one crew were used, the work would probably take about 6 months to complete.
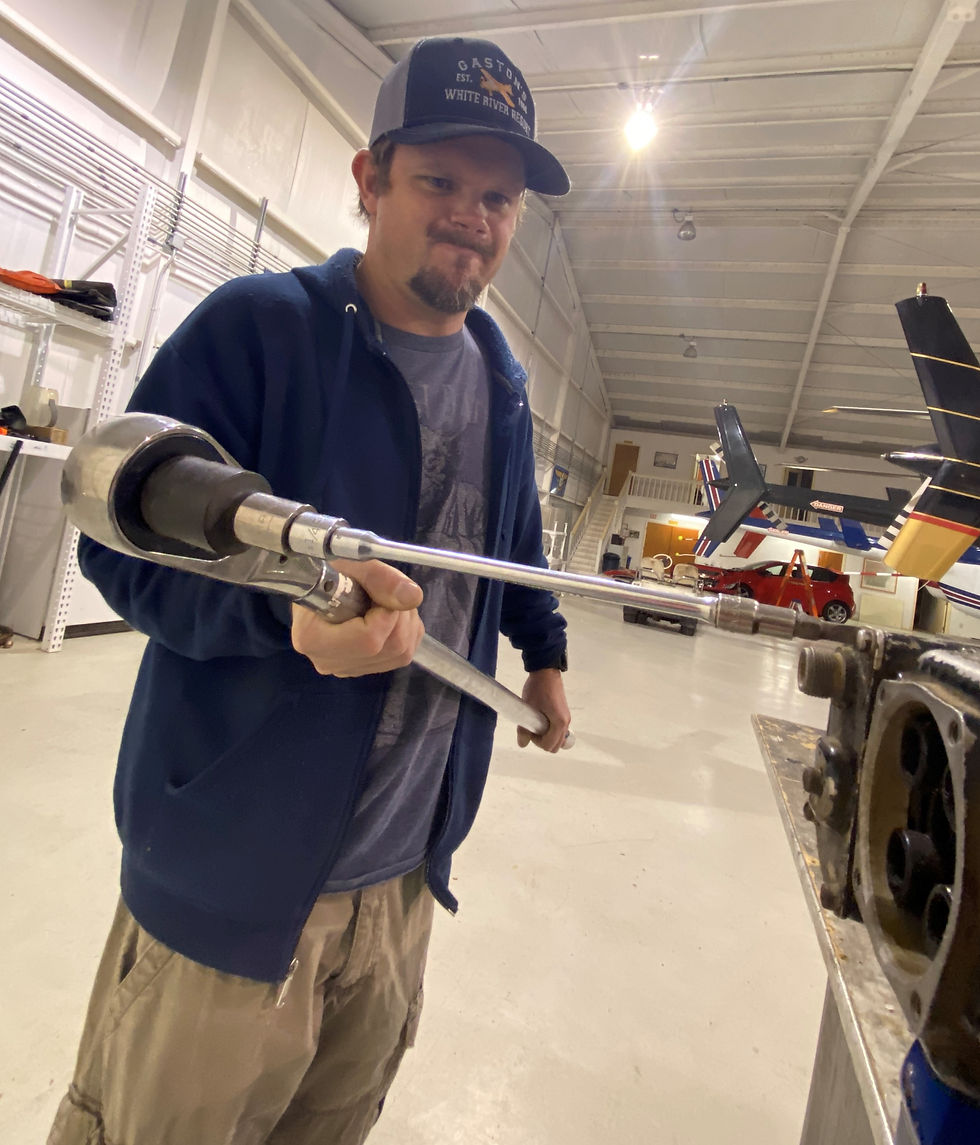
Just as you wouldn’t think of using a 600 ft lb. torque wrench to do the work of a screwdriver, asking the right questions will help you choose the right tool for the job. This is the best practice, which positively affects efficiency, safety, and cost-effectiveness.
Komentarze